Maximizing Tool Life: Understanding Heat and Coolant in Machining
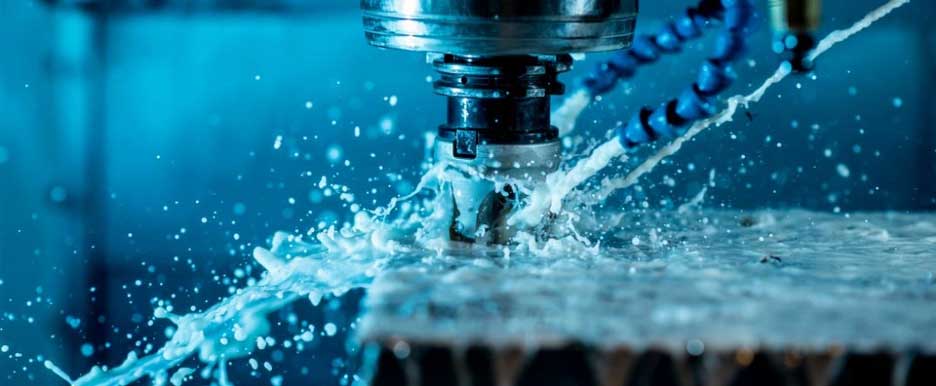
In metal cutting, heat is both a tool’s best friend and its worst enemy. The right amount of heat is necessary and helps create clean, efficient cuts. Too much heat, however, can degrade the cutting edge, shorten tool life, and compromise the quality of the finished part. This balance raises an important question: Should you be machining with or without coolant? The answer depends on several factors, including tool type, material, and cutting conditions.
The Science of Heat in Machining
Heat is a byproduct of machining, generated by the interaction of the cutting tool and the workpiece. The combination of cutting speed, tool geometry, and material properties determines how much heat is created and where it is distributed. When heat remains concentrated in the chip rather than the tool or workpiece, tool wear is minimized and performance improved. However, excessive heat or rapid temperature fluctuations (thermal cycling) can cause thermal cracking of the cutting edges and premature tool failure.
To understand the impact of thermal cycling, consider the sensation of eating ice cream followed by a sip of hot coffee. The sudden temperature change can create discomfort, to say the least. This is similar to the stress a cutting tool experiences when repeatedly exposed to hot and cold temperature cycles.
When to Consider Dry Machining
Certain machining operations can benefit from running dry, particularly when thermal cycling is a concern. The following scenarios often produce better results without coolant:
1. Threading
Single-point threading tools that create standard 60° thread profiles frequently achieve longer tool life when run dry. Coolant can lead to thermal shock and reduce insert performance.
2. Grooving
Shallow grooving operations, such as snap-ring grooves, often see improved tool life when coolant is removed from the equation.
3. Indexable Milling Tools
By the nature of the process, indexable milling tools are exposed to repeated, rapid temperature changes as they enter and exit the cut. Dry machining can reduce the temperature range the tools experience, leading to longer tool life.
4. Short Contact Time in Finish Turning
When a tool is in cut for only a few seconds, such as in light finishing passes, running dry can improve tool life and surface finish. This is particularly true in materials that do not exhibit excessive stickiness.
When Coolant Is Necessary
While dry machining can offer advantages in many cases, some materials and applications require coolant to ensure process stability and part quality. Consider using coolant in the following situations:
- Machining Sticky Materials: Austenitic stainless steels and aluminum tend to produce gummy chips that can adhere to the cutting tool or finished surface. Coolant helps flush chips away and helps prevent built-up edge (BUE) formation.
- Deep Grooving or Drilling: Chips can become trapped in deep cuts. Coolant aids in chip evacuation and prevents recutting, which can damage tool edges.
- High-Temperature Alloys: Heat-resistant super alloys (HRSA’s) generate extreme temperatures during machining. Coolant helps manage heat buildup and lessens work hardening.
How to Test Dry Machining in Your Shop
The easiest way to determine if an operation can be performed dry is to simply turn off the coolant and evaluate tool performance. Start by testing single-point threading operations in alloy steels, finish turning applications with short cycle times, or milling operations where chips clear without coolant flushing.
Monitor for signs of improvement, such as:
- Extended tool life
- More stable edge wear
- Better surface finishes
However, if you notice rapid tool wear, edge chipping, or chip adhesion, reintroducing coolant may be necessary.
Final Thoughts: Heat is Your Ally—Until It’s Not
In machining, heat is a tool’s ally—until it becomes excessive. Understanding when to use coolant and when to go dry is key to maximizing tool life, improving efficiency, and reducing costs. By carefully evaluating your machining processes, you can make informed decisions that optimize performance while protecting your cutting tools. For many applications, turning off the coolant could be the key to unlocking longer tool life and better results.